John E. Dorer is the CEO of eb3.work, a platform that connects employers with foreign nationals seeking to work legally in the U.S. Opinions are the author’s own.
Manufacturing forms the backbone of the U.S. economy, from producing consumer goods to creating essential components for advanced technologies.
Light manufacturing sectors have grappled with an increasingly acute labor shortage. In the National Association of Manufacturers’ first-quarter outlook survey, 65% of companies said attracting and retaining a quality workforce was their top challenge.
Moreover, research from Deloitte and the Manufacturing Institute suggests the industry could need as many as 3.8 million jobs over the next 10 years.
The labor shortage manifests itself in various forms, from needing more entry-level workers to facing a deficit of experienced professionals in specialized fields.
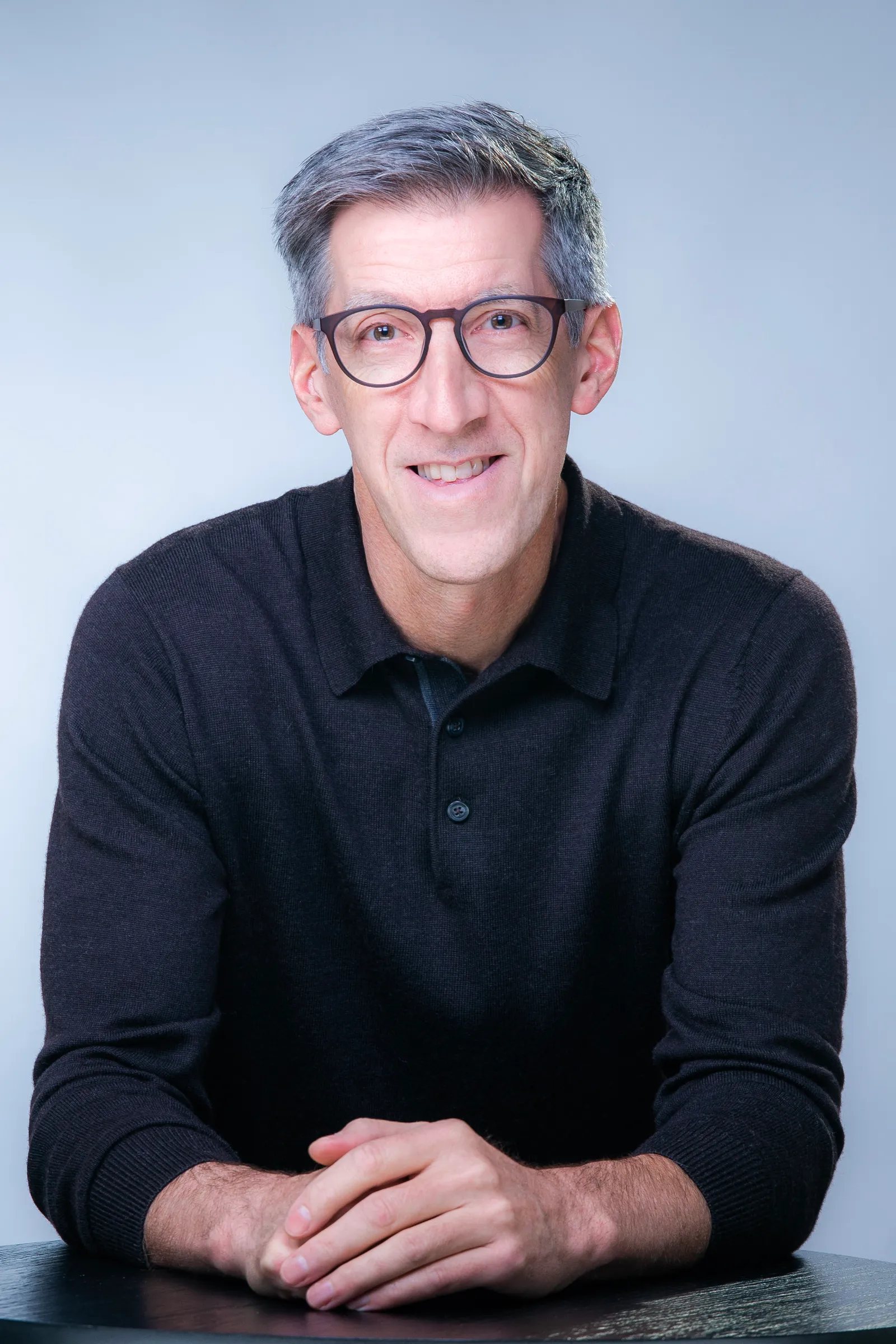
The constraints increase operational costs, decrease competitiveness and shrink market share in an increasingly globalized marketplace. It also hinders businesses’ ability to meet customer demand, fulfill orders promptly and adapt to changing market conditions. And, the ripple effects extend to related industries such as logistics, transportation and retail.
Factors including demographic shifts, changing perceptions of manufacturing careers and technological advancements contribute to the shortage.
It’s imperative that light manufacturers take strategic steps to overcome these challenges. Here are five ways companies can do so:
Workforce development
Workforce development programs can bridge the skills gap and empower workers to thrive in the evolving manufacturing environment by equipping them with necessary skills and competencies.
These programs are designed to foster adaptability and prepare employees for future changes in the company. The programs can encompass apprenticeships, vocational training, on-the-job learning opportunities and partnerships between educational institutions and businesses.
Workforce development can be pivotal in boosting employee morale and improving retention rates. When workers perceive growth opportunities, the result is increased job satisfaction, engagement and loyalty.
Promoting STEM education
Promoting science, technology, engineering and mathematics education nurtures the next generation of manufacturing professionals.
By encouraging students to pursue STEM disciplines and providing hands-on learning experiences, educational institutions can inspire interest in manufacturing careers and equip individuals with the technical knowledge required to succeed in the industry.
Collaboration between schools, universities and industry stakeholders can help align curriculum with industry needs and foster a talent pipeline for the future.
Reskilling and upskilling initiatives
Given the rapid pace of technological changes in manufacturing, reskilling and upskilling initiatives are vital for ensuring the existing workforce remains relevant and adaptable.
The Manufacturing Leadership Council reports that 74% of manufacturing companies are pursuing upskilling of existing workers to address labor shortages, the top strategy cited in a survey.
Businesses can offer training programs, workshops and certifications to help employees acquire new skills, stay abreast of emerging technologies and enhance their job performance.
By investing in employees’ continuous learning and development, companies can boost retention rates, improve productivity and foster a culture of innovation.
Diversifying recruitment strategies
Light manufacturing businesses can benefit from inclusive recruitment strategies that appeal to individuals from various backgrounds and demographics.
For example, despite constituting nearly half of the U.S. labor force, women represent only 29% of manufacturing employees, according to a 2022 Manufacturing Institute report.
Companies can tap into a diverse pool of talent and foster long-term growth by removing obstacles and establishing opportunities for women to excel in typically male-dominated positions.
This may involve partnering with community organizations, supporting initiatives that promote diversity and inclusion and offering competitive compensation and benefits packages to attract top talent.
By fostering a workplace culture of diversity and equity, businesses can enhance employee engagement, creativity and collaboration, leading to a more resilient and dynamic workforce.
Employing foreign workers
U.S. employers who face challenges in finding qualified local workers to fill unskilled positions in light manufacturing may turn to foreign workers.
The EB-3 visa program offers a pathway for unskilled or low-skilled workers to legally immigrate to the U.S. for employment opportunities in roles such as assemblers, machine operators, production workers and similar positions that do not require high levels of formal education or specialized skills.
By sponsoring foreign workers through the program, manufacturing businesses can access a larger pool of potential employees to fill essential roles and support their production processes.
As the light manufacturing industry evolves and adapts to changing market dynamics, businesses must proactively address labor shortages and skills gaps.
By staying abreast of emerging technologies, market trends and workforce needs, manufacturers can position themselves for success in a competitive global marketplace.